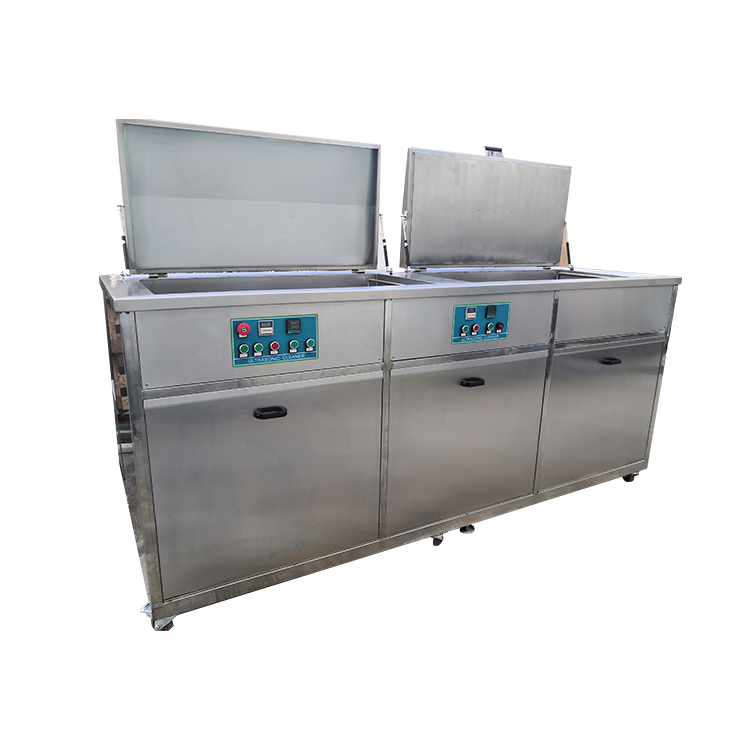
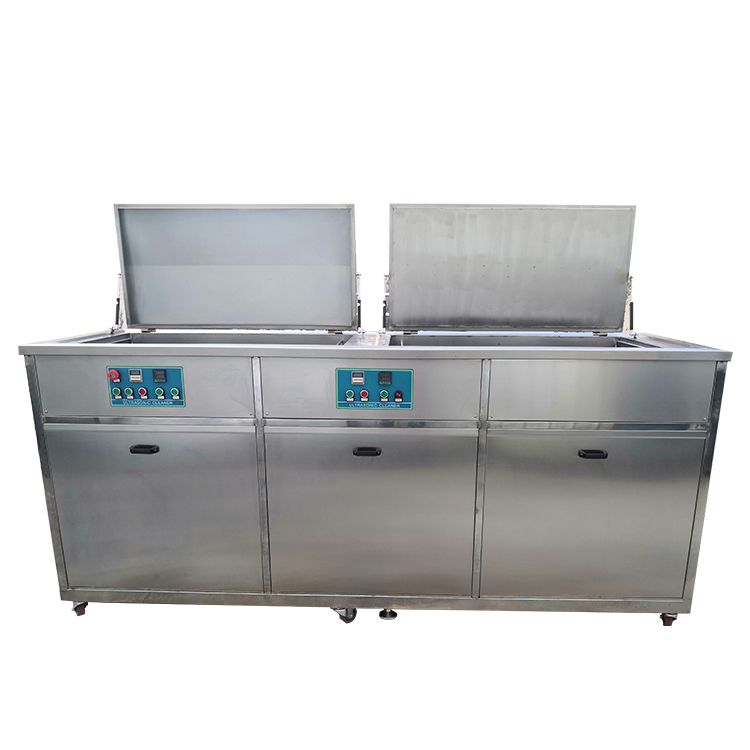
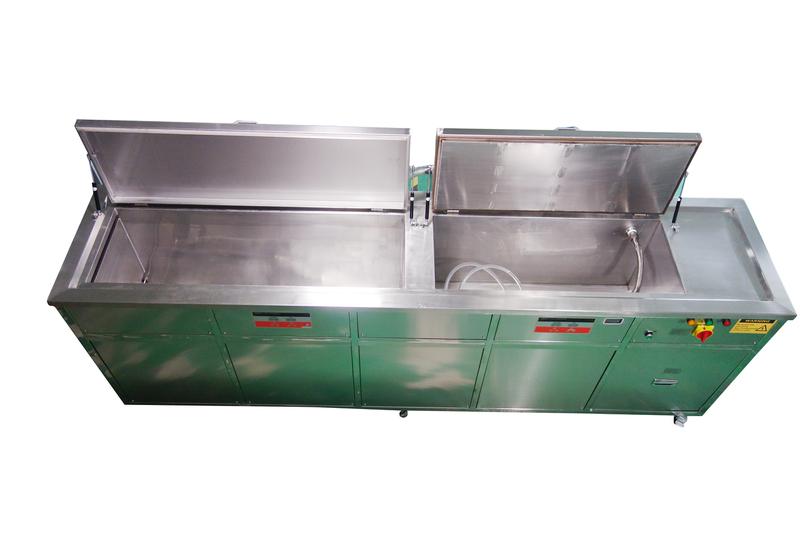
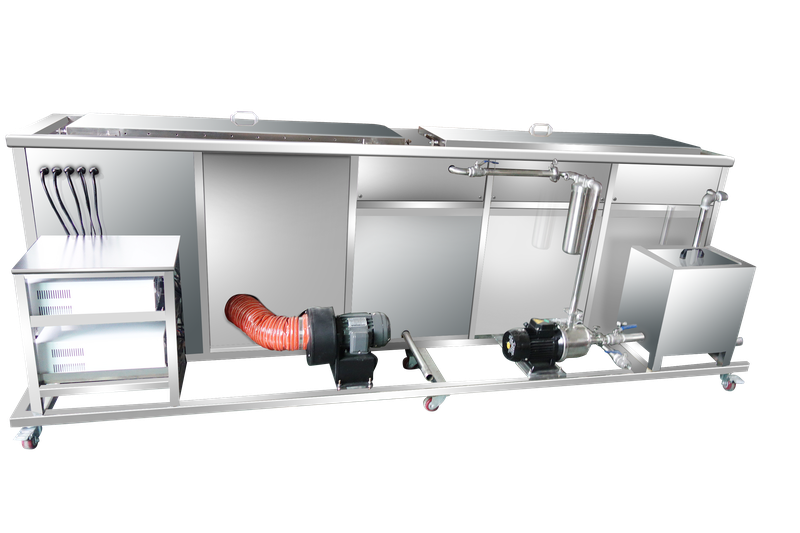
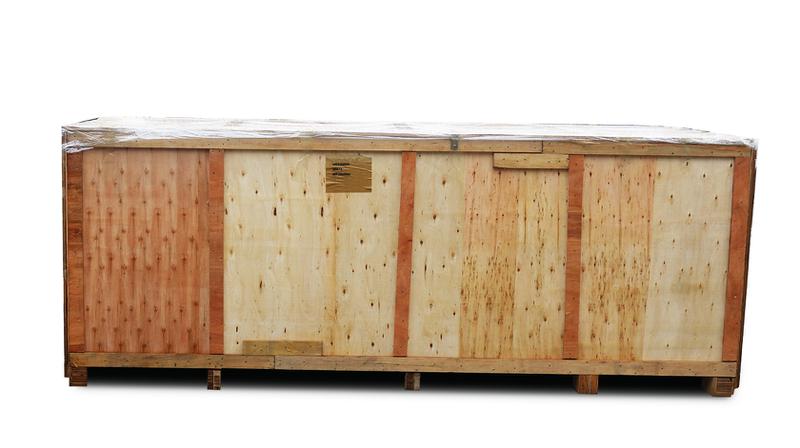
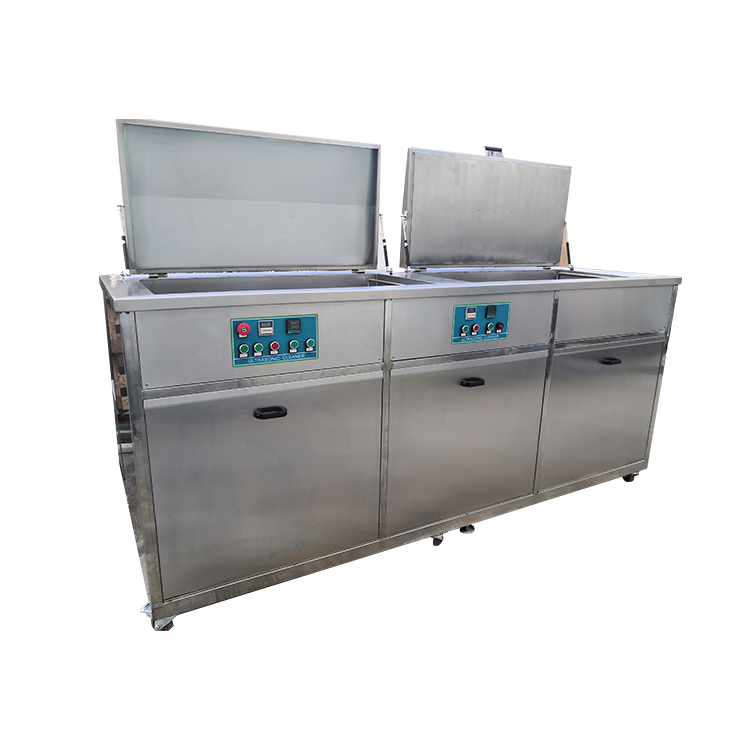
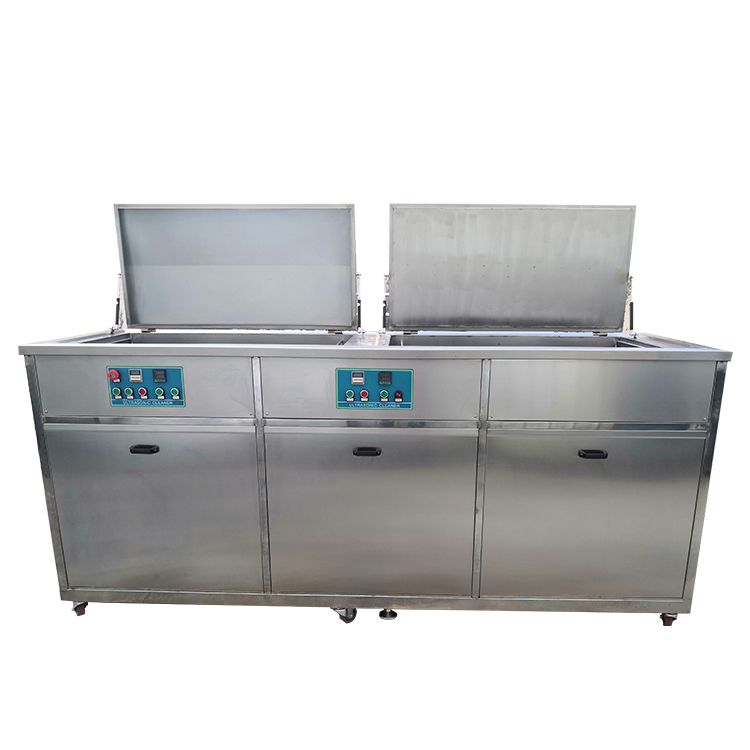
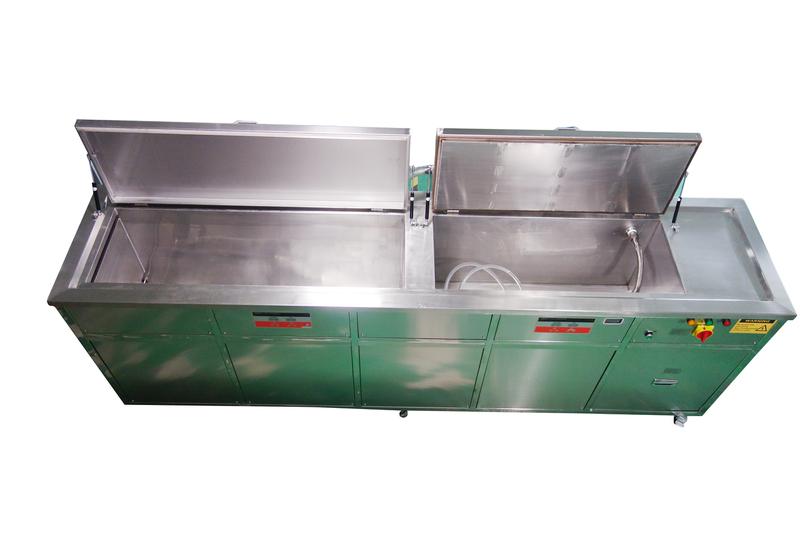
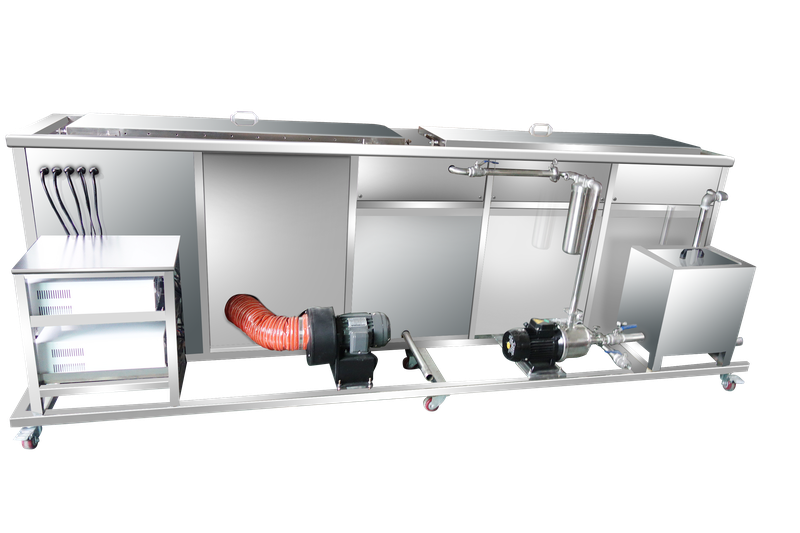
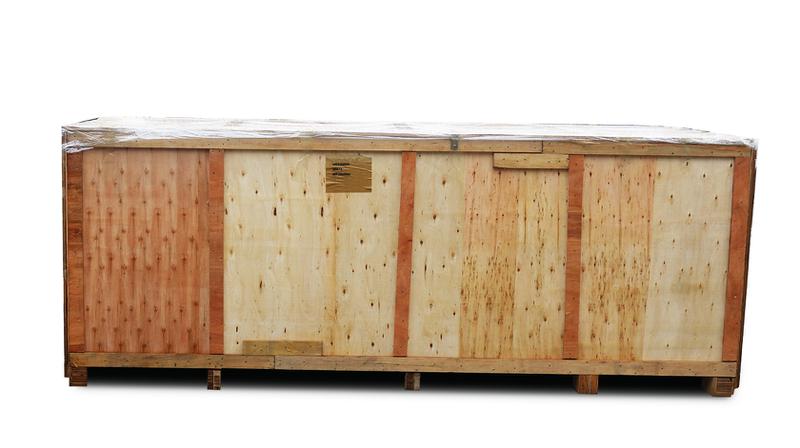
Industrial Ultrasonic Cleaner With Dryer (2 Tanks) With Drying And Filtering
With triple tanks for cleaning and rinsing.
With filtration system.
Multi-direction castors with brake.
1 year warranty.
Industrial Ultrasonic Cleaner Dual tank Specification
Model | T-2060S |
1st Tank Volume | 99L |
2nd Tank Volume | 99L |
First tank size | 500X450X400mm |
Second tank size | 500X450X400mm |
Transducers | 60pcs 50W of every transducer, 30pcs of every tank |
Ultrasonic Power | 3000W 1500W of every tank |
Heating Power | 6000W 3000W of evey tank |
Frenquency | 28KHz/40KHz |
Filtration Cycle System | 1 set |
Generator | 2 set |
Unit size | 1500*1150*850mm |
Packing size | 1560*1210*970mm |
Timer | 0~99 minutes adjustable |
Heater | Room temperature~99℃ adjustable |
Material | SUS 304 default, can be SUS 316 |
Power Supply | AC 220V 3 phase ; AC 380V 3 phase |
N.W. | 250KG |
G.W. | 280KG Wrapped by film in wooden case |
Lead time | 18 working days |
Warranty | 1 year warranty period, technique support all time |
Certificates | CE, RoHS, FCC, |
Advantage | Filter the dirty water; keep the water clear in tank; lower the frequency of changing water |
Industrial ultrasonic cleaner 104liters with drying tank
500X450X400mm , frequency 28kHz
(available in 40 kHz) - SUS 304 / 316L stainless steel quality -
Equipped with an external frequency generator to deport the electronics
Tank 1: Ultrasonic cleaning
ULTRASONIC POWER 2500 Watts peak
30 transducers 28kHz - 1500 watts effective
External frequency generator with power adjustment
Stainless steel tank 500X450X400 mm (int. Dimension LxWxH)
2mm stainless steel thickness (SUS304 / 316L quality), very strong welded tank
Sus304 stainless steel frame equipped with braked castors
Timer integrated in the control panel with memory and digital display of the remaining time
FAST heating power 3000 Watts
thermostat on the front of the tank
Temperature adjustment from 0 to 80 ° separate from the use of ultrasound
Stainless steel drain valve, quick drain
Very reinforced stainless steel basket for heavy parts
Tank 2: Forced air dryer
SUS304 / 316L quality stainless steel tank, possibility of blowing cold air or hot air
Heating power 3000 Watts
High power wind tunnel
Digital timer with automatic shutdown
Reinforced stainless steel basket
Our multi tank ultrasonic cleaning systems combined with the hot air dryer can be used as an effective part cleaning line by housing heated cleaning solution, cascading DI rinse water, and a final cascading DI rinse water with a final hot air dry step. The process would move from left to right: the parts would be cleaned, rinsed, rinsed and then dried.
The clean tank can be optionally equipped with pump filter systems which provide 5 micron filtration of the alkaline cleaning passivation solution. The common configuration shown is 3.5 gallon tanks, but any size tanks can be used in similar configuration use.
For applications requiring multiple ultrasonics frequencies (28 kHz, 40 kHz, 80 kHz, 120 kHz, etc), the floor standing ultrasonic console cabinets are fully customizable per customer requirements with multiple ultrasonic cleaner and ultrasonic rinse tanks. Each tank is individually digital timer controlled with digital temperature controller for tank heats from 80F to 180+F. The ultrasonic cleaning system is fully customizable to any configuration of tanks: wash, overflow rinse, passivation, acid etch, etc and layout.
Multi stage ultrasonic claner Specifications:
Model | T-3048G | T-3072G | T-3144G |
Ultrasonic Tank Dimension(mm) | 550X400X350 | 600X500X450 | 1000X600X600 |
Rinsing tank dimension(mm) | 550X400X350 | 600X500X450 | 1000X600X600 |
Drying tank dimension(mm) | 550X400X350 | 600X500X450 | 1000X600X600 |
Max. Capacity | 77L/tank | 135L/tank | 360L/tank |
Construction Case | SUS304 (Mirror shining image available) | ||
Construnction Tank | SUS304 | ||
Transducer Number | 48pcs | 72pcs | 144pcs |
Ultrasonic power(Max.) | 2400W | 3600W | 7200W |
Ultrasonic frequency | 40kHz | 40kHz | 40kHz |
Temperature range | 20~80C adjustable | ||
Heating power | 6KW | 12KW | 24KW |
Timer | 1~99h | 1~99h | 1~99h |
Drain | 3/4" Valve | ||
Lid & Basket | Available, material: SUS304 | ||
Cleaning Tank voltage | AC220V/AC380V 3phase | ||
Generator Voltage | AC110V / 220V 1phase | ||
Features | With triple tanks for cleaning and rinsing. With filtration system Multi-direction castors with brake; 1 year warranty |
Removes brake dust, rust, grease and all dirt and gives surface without grease and fingerprint
Clean your clients' wheel easier and more efficently than ever before with this ultrasonic cleaning system! This technology can be adapted to clean other parts and accesories like engine parts,gearbox parts, etc. It saves you time and money! After the cleaning it's much easier to find any hidden damages on the surfaces!
Here is the work cycle :
•Ultrasonic cleaning in warm alkaline detergent
•Rinsing in cold running water
•Rinsing with ultrasonics in warm demineralized water
•Drying in warm pressure-ventilated air
Step 1: Cleaning:
The first stainless steel tank is used for ultrasonic cleaning, and includes the components required to remove contaminants from part surfaces. For the best results and for most applications, we recommend our patented multiple frequency ultrasonic system.
A high-efficiency heater is used to heat the ultrasonic cleaning tank which features a digital temperature controller so that bath temperature is continuously displayed.
Particles and contaminants are automatically removed by means of AGSONIC's particulate filtration system – thus helping to increase the longevity of the cleaning agent. Filters are conveniently housed for easy removal and servicing. Surface skimming options are also available to prevent re-deposition of contaminants back onto parts when removed from the tanks.
Finally, the ultrasonic cleaning cycle is switched off when complete by means of the digital ultrasonic timer which comes as a standard feature of both MTC-4 systems, or by the included optional Automation Systems.
Steps 2 and 3: Rinsing and/or rust prevention:
Most commonly, the second and third stainless steel tanks are used for primary and secondary submersion rinsing operations.
In this configuration, the system can provide zero-residue cleaning results when the second rinse tank is supplied with purified or deionized water. In rinse/rinse configurations, tanks are designed in Reverse Cascade Overflow Format which greatly reduces the consumption of water since both rinse tanks share the same water supply.
In clean/rinse/rust dip/dry systems the second tank can be manufactured for use as a dipping bath for immersing parts in rust preventative fluids to prevent corrosion of such parts.
Step 4: Drying:
The fourth tank features a partially-recirculating, high volume drying system. This includes a core electric heater and blower that direct hot air straight to the cleaned parts, thus maximizing drying speed. Parts are dried more by air volume than by excessive heat which means that operators can handle parts baskets soon after completion of the drying process, without the need for a lengthy cooling period. The system also includes a 4" gated exhaust to channel moist air out of the drying tank and a stainless steel cover to keep the drying environment contained. A specifically designed air duct system prevents liquids from entering into the system.